Working in manufacturing is all fun and games until the kief particles are filling the air and coating not only the pre-rolls but also the operators, right? It’s no secret that without the proper technology, manufacturing centers can be hazardous places. Luckily, technologies like automation, the internet of things (IoT), and artificial intelligence (AI) are adding a new layer of workplace safety. How? Let’s get into it.
First, automation. Already, automation offers significant safety benefits across a variety of processes. For example, instead of workers manually dispensing heated liquid to fill vape carts, the process can be automated within a contained system. This reduces the risk of repetitive strain injuries like carpal tunnel syndrome and eliminates the potential for contamination from human contact.
More importantly, automation creates a safer workplace because it enables operators to control the environment. Take the kief-coating example from earlier: After human operators roll joints in kief on open tables, they must brush the excess off the tabletops and sweep it up from the floor. That can cause the fine dust to become airborne, which creates a breathing hazard for humans. Instead, automated systems can enclose the process, capturing and containing any airborne materials while a machine coats the joints.
In the near future, I expect to see an increase in the adoption of automated machinery that contains the coating process within a volume, applies a vacuum, and filters the air, thus leaving humans breathing room that is free from any unwanted particles. The automation in this scenario protects workers from inhaling harmful substances and ensures products like pre-rolls and concentrates remain free from bodily fluids or other contaminants that could be transferred by hand.
Remediation is another key area in which automation can create safer workplaces. Ozone- or UV-based remediation treatments are extremely dangerous to perform manually, but automation enables remediation that otherwise would be impossible due to the high human risk involved.
Next, IoT. Essentially, the internet of things is a network of interconnected devices that exchange data with each other via the cloud. In manufacturing, IoT benefits operators by providing deep insights into production flow rates and identifying production failures. When all manufacturing machinery is connected and something goes wrong, real-time surveillance allows safe, remote troubleshooting to get production back on track.
IoT also enables robust data analytics, providing operators with a reliable source of truth stored in the cloud rather than on a clipboard. I’ve seen many instances where companies replace manual processes—like having employees sign off on results—with automated online dashboards. This transition not only smooths out operations but also significantly enhances efficiency.
“But,” you ask, “how can IoT provide a safer work environment?” Here are a few ways:
- Certain IoT sensors can detect harmful levels of particles or contaminants in the air and alert the proper authorities that action must be taken to protect workers.
- IoT-enabled machines offer real-time data about their operating status, allowing for predictive maintenance and reducing the risk of accidents caused by equipment failure.
- IoT’s ability to execute track-and-trace functions at the machine level greatly reduces the number of errors that must be reported under Marijuana Enforcement Tracking Reporting Compliance (METRC).
In the future, I expect IoT systems will connect directly to compliance software. If this becomes a requirement for our industry, manual data entry could be eliminated, reducing the risk of human error and ensuring adherence to safety and reporting standards. Consider this example: When you write production data on a clipboard, there’s a risk of human error. Say someone writes a numeral one that looks like a seven. Not only will this cause significant discrepancies in reporting, but the error also could lead to operational mistakes.
Machines don’t have messy handwriting or make calculation errors. IoT devices capture and store data accurately, abstracting it to a database rather than leaving the process to chance on the shop floor.
Lastly, let’s look at AI. Today, AI serves as a significant quality-control check in the manufacturing process, which can enhance safety measures. Technology like computer vision can pattern-match to discern between passing and non-passing material.
For instance, a human inspector might miss a structural issue like a cracked glass tip. However, computer-vision systems don’t become distracted or suffer momentary vision lapses, so they identify defective items every time, thus protecting workers from cuts and end users from finding broken glass in the products they purchase.
In some cultivation facilities, machine-learning algorithms, a form of AI, are used to balance carbon dioxide (CO2) and sulfur levels. Overfilling a room with CO2 can be hazardous, and manually managing levels is risky. Combining AI algorithms with IoT devices programmed to control CO2 and sulfur levels significantly reduces the risk of failure.
As our industry grows, there will be a greater demand from the government and other regulatory entities calling on manufacturers to ensure workplace safety. Therefore, cannabis manufacturing is in a unique position to lead a novel approach to workplace safety with the integration of automation, IoT devices, and AI. Unlike older industries like food manufacturing, which would face costly retrofits, cannabis facilities are being built with IoT and automation capabilities from the start. While the industry is still operating on a small scale due to federal legality issues, as it scales up, facilities with large build-outs likely already will be fully integrated with automation, IoT, and AI.
The question is, how will you prepare for the new frontier in manufacturing and workplace safety?
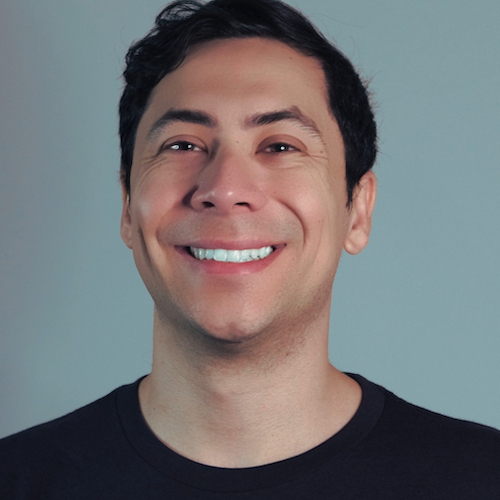
Serial entrepreneur Nohtal Partansky is founder and chief executive officer at Sorting Robotics. Previously, he was an engineer on the NASA Jet Propulsion Laboratory’s MOXIE team. There, he helped develop an instrument currently sitting on the surface of Mars and producing oxygen from the atmosphere. Sorting Robotics builds innovative AI-driven machines for cannabis manufacturers and vertically integrated brands.