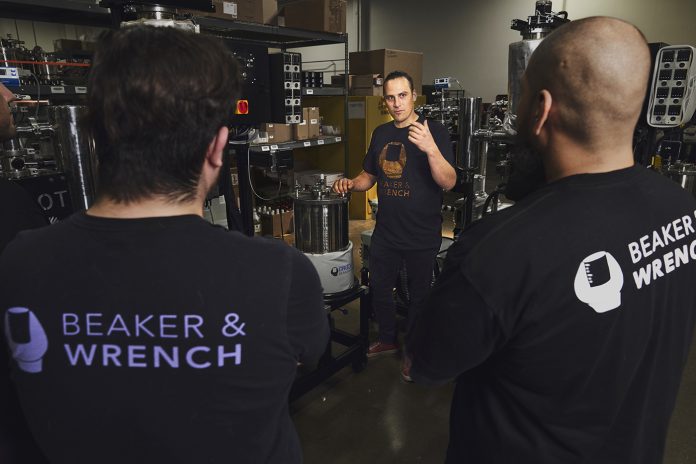
As the cannabis industry matures, so do the solutions to help extractors operate more efficiently and produce a higher-quality product. Now more than ever, oil manufacturers must stand out from the competition while simultaneously running dynamic, growth-oriented operations.
Beaker & Wrench has been helping to elevate the extraction space since its inception in 2016. Founded by engineer Ace Shelander and chemist and lab operator Lilibel de la Puente, the company offers a wide variety of products for small and large facilities alike. The company’s wiped-film distillation machines, new solvent-recovery system, dosing pumps, and “steelhead” short-path condenser are trusted by extractors aiming to create the best possible oil.
Beaker & Wrench initially found success with after-market dosing pumps, a product the company developed to meet an urgent in-house need. “Lilibel was operating a small wiped-film system and didn’t have a dosing pump, which is an incredibly important accessory for these machines. It’s in constant operation,” recalled Shelander, the company’s chief executive officer and head engineer. “I couldn’t find one that I was confident would do the job, so I custom-designed one from scratch. It tripled the output of the machine. Ever since then, we’ve been solving every pain point we can find in the distillation process.”
The pair soon set their sights on developing their own wiped-film machines, using their practical expertise to build six-inch and twelve-inch models that produce 90- to 95-percent-pure distillate. The machines, constructed with fully compliant USA NRTL-certified components, achieve an output of three to fifty liters per hour. The initial successes left the team ready to go the distance.
“From the very beginning, our goal was to provide equipment that was efficient and reliable right off the lift-gate, which is something we felt our competitors didn’t offer,” de la Puente, Beaker & Wrench’s president, said.
Since the dosing pump’s launch, Beaker & Wrench has been in a continual state of ideation and innovation. Demand for cannabis oil is steadily increasing and by 2025, Grand View Research expects vape products to reach $2.2 billion in worldwide sales. Knowing this, the Beaker & Wrench team has made it their mission to develop a suite of solutions aiming to revolutionize, not merely evolve, the extraction space.
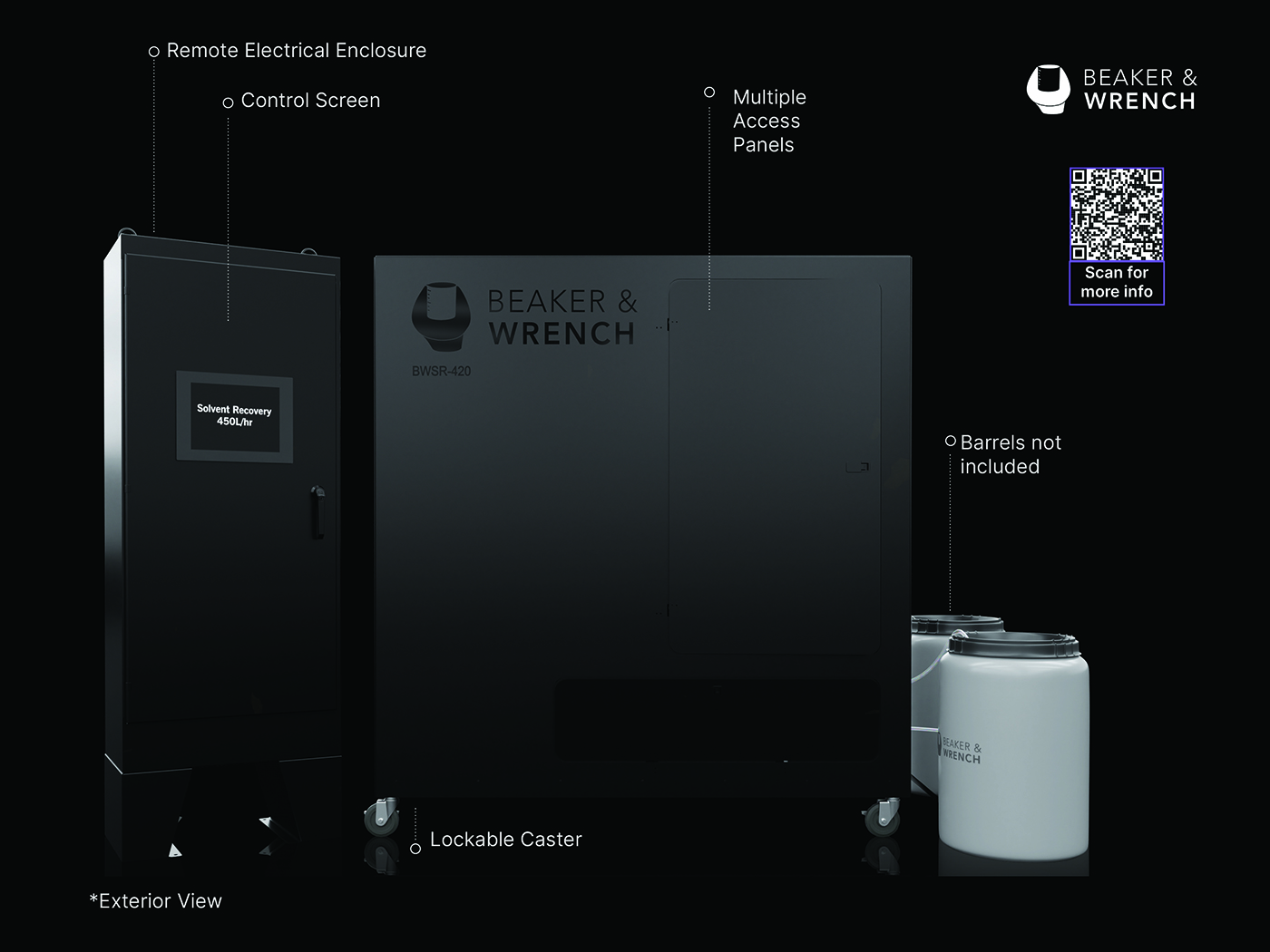
A new solvent-recovery system is the perfect example, as it was specifically designed to cut costs and increase output.
“What’s really special about it is that the system uses a closed-cycle heat pump, which saves 80 percent of the energy compared to a falling film,” Shelander said.
The solvent-recovery system is sleek and powered by self-regulating automated technology. Its streamlined feed and recovery system can process up to 450 liters (120 gallons) of ethanol per hour, leaving less than 1 percent of residual solvent in the oil.
Running the solvent recovery system can save up to $5,000 per month in electricity costs and allows that electrical service to be allocated to other parts of the process, which increases the total output. The Beaker & Wrench solvent-recovery machine is a fraction of the size of similar systems and can fit through a standard-size door.
While these systems are designed for larger-scale operations, Beaker & Wrench is developing similar systems for craft manufacturers. The team recently introduced a new steelhead component for short-path systems, which can be retrofitted to standard equipment. The part is suited for smaller extractors that aren’t quite at wiped-film scale but are ready to kick things up a notch.“We’re excited to begin offering a reliable and efficient solution for smaller-scale distillation processors who are trying to grow their business and potentially get into large-scale processing,” de la Puente said.
The steelhead is an impressive time-saving tool. An average short-path distillation machine takes six to sixteen hours per batch, but the new steelhead reduces that to as little as half the time, which reduces operator fatigue and labor use and increases production capacity.
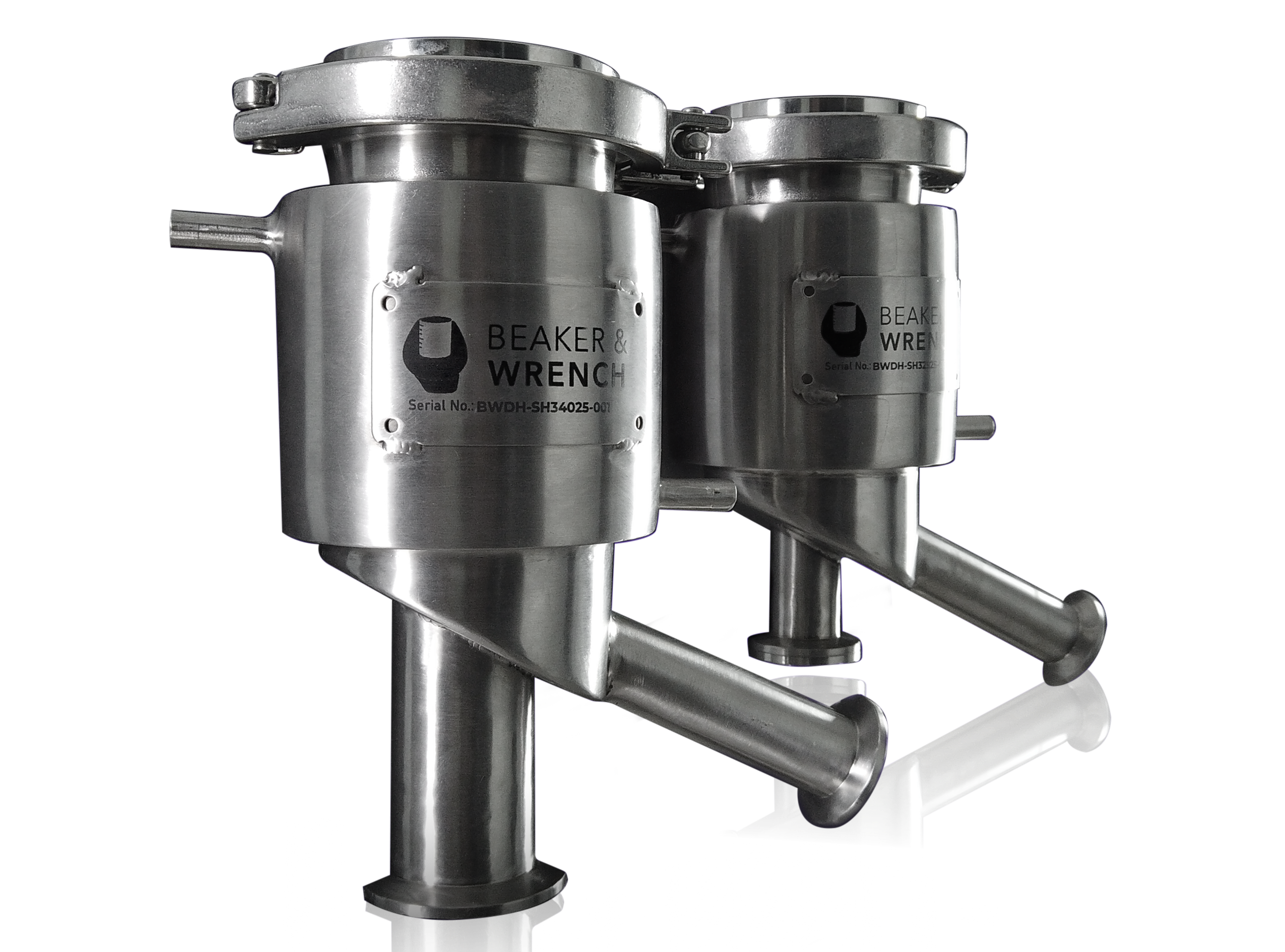
“It literally saves hours and hours per day for the operators that are running these steelhead systems,” said Shelander. “It’s a short workday instead of something long and drawn out.”
Already an established leader in the space, Beaker & Wrench continues its path toward providing a complete solution for extractors of all sizes. By building energy-efficient systems that take up smaller footprints in facilities, the company is able to help its customers do more with less. By helping extractors create purer oils at a fraction of the cost, Shelander and the team hope to have a resounding effect on the trajectory of the marketplace as a whole.
“We’re trying to help people produce the best product they can and improve the processes and the industry,” he said.