For employees working in the cannabis industry’s licensed facilities, disposable or single-use gloves are a prerequisite for handling the plant. Especially for those working in the cultivation and processing sectors, durability is more than a passing concern. Rips and tears can be incredibly frustrating for glove-wearers working with intricate products that can be equal parts sticky and prickly.
Much like the products they are employed to handle, gloves come in varying degrees of quality and chemical composition. The most common categories are industrial-grade, food-handling, and medical-grade, and each adheres to its own Acceptable Quality Level (AQL) score, a benchmark for measuring pinhole defects. The lower the AQL rating, the better the glove’s quality.
The “industrial” in industrial-grade does not indicate a hardier product. In this case, the label indicates the gloves haven’t been subjected to inspection or specific testing requirements.
Food-handling gloves must comply with United States Food and Drug Administration regulations (FDA Title 21 CFR Part 177). Raw materials must be of “substances generally recognized as safe for use in food or food packaging.”
Medical-grade gloves are subjected to a battery of technical tests to meet FDA-regulated safety requirements. To pass inspection, medical-grade gloves require an AQL score of 2.5 or lower—which means a maximum of 2.5 gloves with pinhole defects per 100.
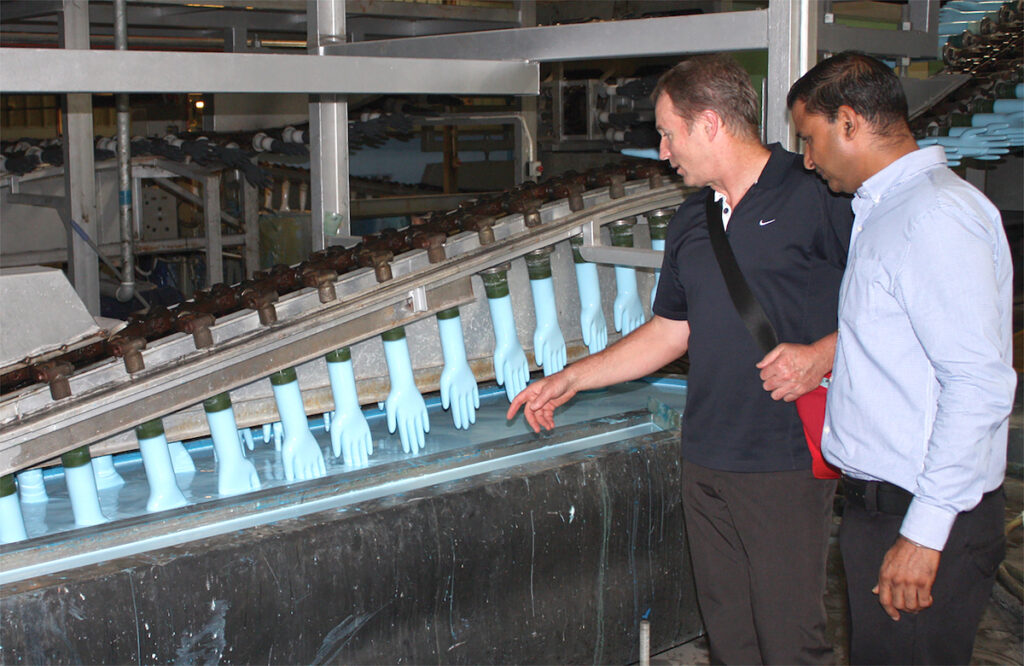
The primary determinants of glove resistance to tearing or ripping are the raw materials used in the manufacturing process. Many users are under the misguided notion a thicker glove is better and won’t tear as easily. However, inexpensive gloves are produced with fillers including carbon black, silica, and even chalk in order to decrease manufacturing costs. Chalk doesn’t stretch, which is a huge problem since elasticity is a major component of a glove’s strength and quality. Ingredients matter, considering raw materials are responsible for almost half (45 percent) of total production cost.
Thicker gloves on the low end of the quality spectrum are less elastic than a high-quality, thinner glove. How so? Repetitive hand movements—like those used in the intricate bucking and trimming stage of cultivation—strain the elasticity of disposable gloves, leading to the all-too-common rips and tears that force wearers to disrupt their workflow, abandon their torn gloves, and begin again with a fresh pair. When these incidents become frequent, the opportunity cost of buying an inferior glove can significantly impact productivity. In addition, inferior products create excess waste, disposal cost, and potential cross-contamination. They also put a crimp in sustainability efforts.
Cross-contamination from disposable gloves can compromise the purity of cannabis products. Cheaper gloves, in which the raw ingredients are composed of lesser materials, can emit a high chemical toxicity conducive to unwanted bacterial contamination. Gloves aren’t evaluated for cleanliness (either at the microbial or bioburden level), raw-material toxicity, chemical composition, or pathogen contamination. In several recent cases, these and other microbiological hazards present in the manufacturing process were traced back to gloves, resulting in expensive product recalls.
Glove-wearing is essential to numerous production stages in a cannabis operation. Because tasks like growing and harvesting plants are much more labor-intensive than processing tinctures and edibles, gloves in a variety of thicknesses may offer a better all-around solution for comprehensive operations than a one-size-fits-all product. It’s not unheard of to track and assess glove performance within an operation. Keep track of rips, tears, and failures—as well as at what stage of production they occur—and see if the data reveals a need for higher-quality gloves in specific phases. Reputable and knowledgeable suppliers should welcome the opportunity to arrange glove trials, allowing organizations to assess the optimal grade and quality for all operational practices.
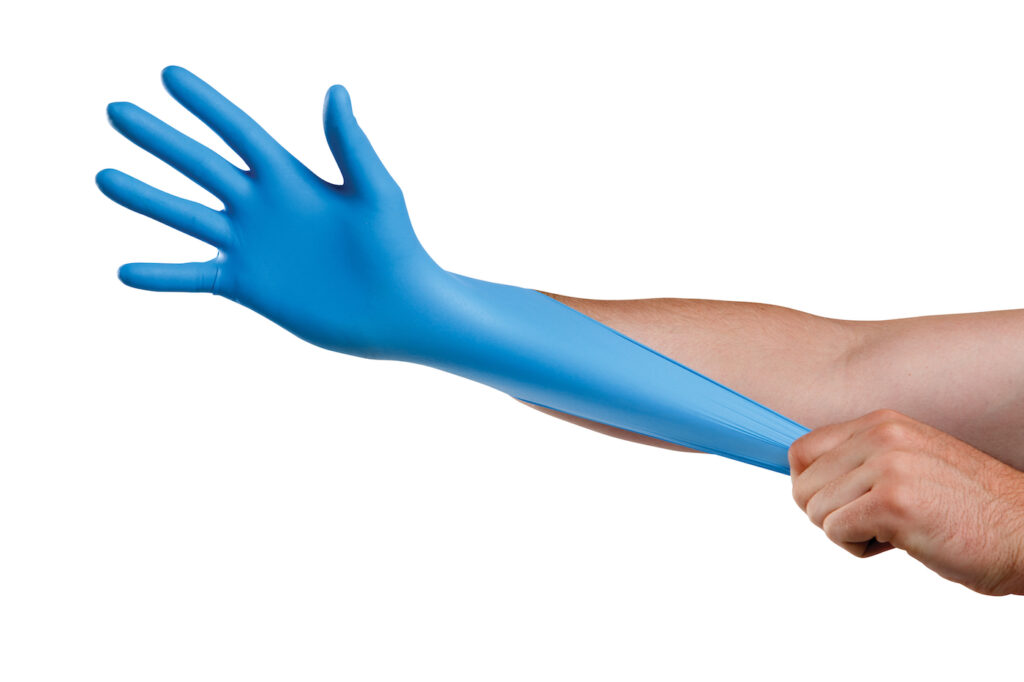
In summary, remember: Thicker doesn’t always mean stronger. Lower quality means less elasticity, and the raw ingredients used in the manufacturing process determine the strength and quality of disposable gloves. Furthermore, different tasks or production stages may require different glove grades. Untested and unregulated gloves increase the risk of cross-contamination and potential recalls.
No disposable glove is indestructible, but you’ll never go wrong choosing quality over cost.

Steve Ardagh is founder and CEO of Eagle Protect, a disposable- glove supplier dedicated to responsibly sourcing quality products for customer safety and risk mitigation. After establishing Eagle Protect as an industry leader in New Zealand, he relocated to the U.S. in 2016 and launched Eagle Protect PBC, bringing with him Eagle’s mission to provide products that are certified food-safe, ethically sourced, and environmentally sound.