Standardization occurs when the majority of businesses in an industry adopt the same processes or create certain products in a shared, consistent manner. Consider a box of cereal, for example. I guarantee no matter which brand you choose, each box will open in the same way.
In the cannabis industry, we’re seeing standardization steadily spread across product categories. One major catalyst is automation. By streamlining production from cultivation to processing to retail packaging, automation ensures consistency at all stages, thereby establishing standardization from seed to sale.
Automation simplifies what once was a major bottleneck for retail brands: packaging. Years ago, each operator had to figure out its own best way to package and display flower and pre-rolls. Today, the industry has a better understanding of the types of packaging that work best for each product and for consumers, adding a level of consistency that makes manufacturing easier and less time-consuming.
That’s especially true now that packaging has become relatively standard for some product types. For example, in today’s dispensaries approximately 90 percent of gummies and about 80 percent of flower are sold in bags. Remember the early days when flower was displayed in enormous jars? Bags are easy to machine-fill, ship, hold in inventory, and hang on store shelves. It’s also easier to machine-print information directly on individual bags. Additionally, bags offer more space for compliance labels, which will be especially important when the plant becomes federally legal. Standardization like this relieves retailers’ headaches and also enables easy product recognition by consumers.
Automation also helped bag sealing and printing take a big step forward. When humans are sealing or writing important data on bags, errors can and do happen. This not only leads to an inconsistent consumer experience but also can cause compliance issues. Automation helps ensure seals are accurately closed, avoiding the melting of zippers or uneven heat stamps. For printing, automation speeds up the process, making sure all packages are labeled correctly.
Weight consistency, too, received a major boost from automation. If a bag claims to have ten gummies inside, there had better be ten gummies in that bag, right? Or, if a pre-roll tube states the enclosed joint contains one gram of flower, there had better be one gram of plant material inside. Automated weighing ensures the product accurately matches the label. This enables business owners to predict and control product loss within a 10-percent variance—a stark contrast to the unpredictability of manual packaging.
Child-resistant technology is required for most cannabis packaging, but depending on the type of packaging—such as cartons with hidden tabs and multiple steps to access the contents—automating packaging processes can be challenging due to the numerous touchpoints involved. That’s why many companies have adopted bags with child-lock zippers and jars with child-resistant features that are easily compatible with automated packaging machinery. In this case, automation is leading the movement toward more uniform, safe, and standardized practices.
Automation also enables businesses to scale. Typically, one machine can do the work of eight to twelve people. Small companies with five or fewer employees devoted to manual packaging could double their capacity by adding a single machine. For example, with three people and automated technology, a manufacturer could package 10,000 to 20,000 bags of gummies, edibles, or flower daily—a task that would take a dozen people a week or more to complete manually.
Automation reduces labor costs and increases productivity, leading to increasing scalability and, of course, standardization. The more automation businesses bring into their processes, the more uniform products will appear across brands.
Today, operators prioritize automation from the jump, recognizing the immediate benefits mechanization can bring. Automation will become just another normal part of business plans as standardization increases. Likewise, as the adoption of automation rises, standardization will become much more established in our industry.
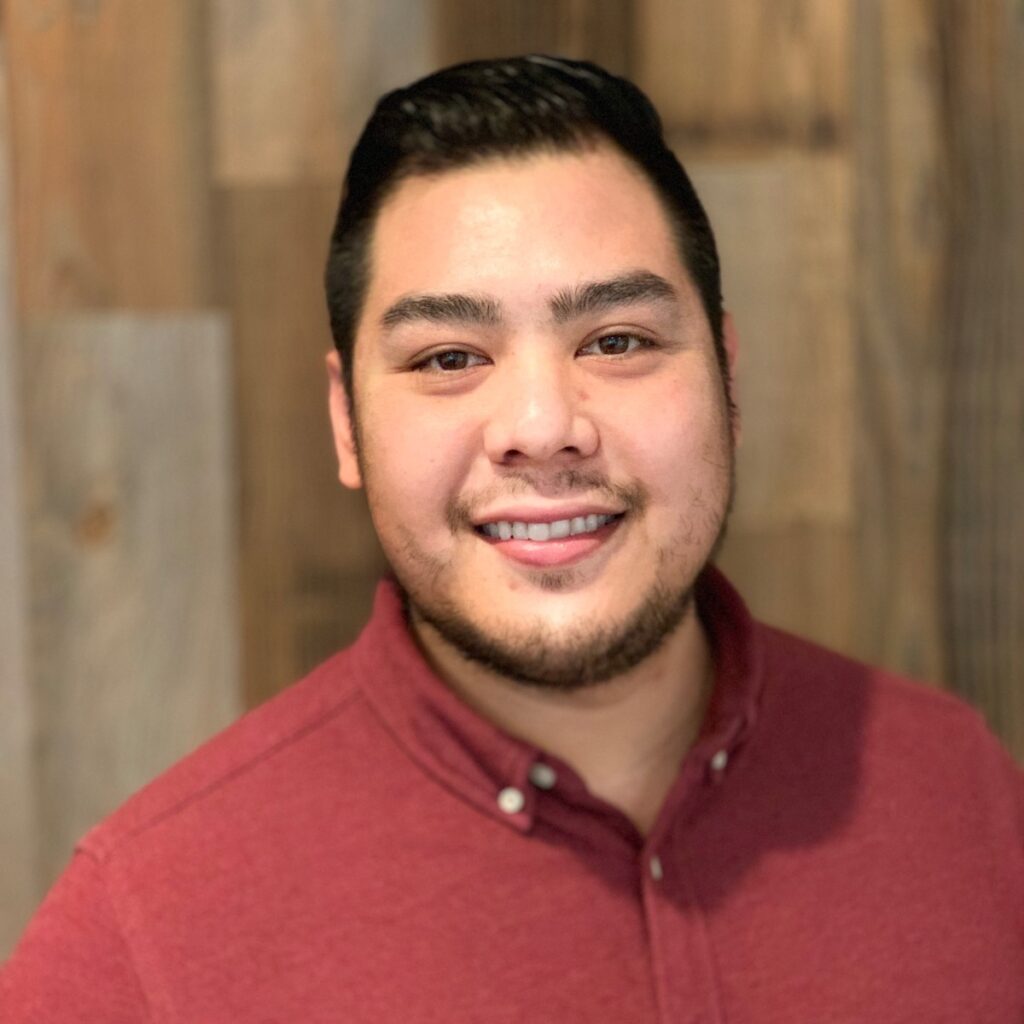
Alain Vo, chief executive officer at automation machinery supplier LeafyPack, has spearheaded advancements in packaging technologies for the past five years. He focuses on enhancing output speeds and integrating innovative features while upholding world-class service standards. Previously, he contributed to the development of LED grow lights.